Turnkey Systems
Engineering and Design
Dantco has designed layouts for mixers and dispersers considering the structural
characteristics of the plant, has made structural modifications to suit the
new and existing equipment with emphasis on product flow, has designed working
platforms and skidded systems to increase production efficiency, has designed,
specified and selected piping systems including valves, filters, pumps, motors,
flow meters, instrumentation for product flow and hot oil heating, has designed
and selected motor controls, including starters, variable frequency inverters,
push button stations, remote speed controls, hydraulic, pneumatic and
thermo controls as applied to mixers, dispersers, homogenizers, and ribbon
blenders. All plant layout, piping, platforms, fumes and dust collection,
and electrical controls were designed and selected within the applicable
environmental constraints.
Installation and Integration
Dantco has installed and integrated various mixers and dispersers systems,
used and new, including structural modifications, rigging and set-in-place,
hydraulics and pneumatic lines, water lines, hot oil lines, electrical connections
and hook-up. Dantco personnel are well adept to do plumbing, millwright,
iron works and erection, demolition and masonry, and electrical.
Validation
Dantco has conducted in-house and at customer facilities acceptance tests
of mixers, dispersers, homogenizers, ribbon blenders, mixing tanks, storage
tanks, jacketed tanks, conveyors, tank presses, heating/cooling, dust prevention
and collection, can crushers, bag bailers, using calibrated equipment and
instrumentation to assure that the equipment met or exceeded the designed
parameters.
Dantco is also able to conduct system tests to assure that the production
line performs to the designed specifications.
Dantco test conductors and technicians are continuously instructed to keep-up
with the state-of-the-art.
Examples
Turnkey
Production Facilities
Turnkey
Process Piping
Turnkey
Working Platforms
Turnkey
Mixing System
Portable
Air Mixer/Tank System (1) (2) (3) (4)
Series
2072 System (1) (2)
This set-up shows 3 mixing stations
with variable speed dispersers, remote control panel, mixing tanks,
transfer pumps and piping, air supply manifold, drain tank all mounted
on a heavy duty platform. This system is used in explosion proof area
to process plastic compounds. The disperser on the right (Model DVF-300-48/21-EX/SS)
has a 30 HP inverter duty motor with fixed sheaves and belts transmission
controlled by vector drive and remote panel displaying mixing shaft
speed and motor amperage and including on/off switch, E-switch and
speed potentiometer. The mixing vessel (Model PTA510-SS) has a capacity
of over 500 gallon. The other 2 dispersers (Model DVF-100-48/21-EX/SS)
have 10 HP inverter duty motor and similar transmission and controls.
The mixing vessels (Model PTA-55SS) have a capacity of over 55 gallon. |
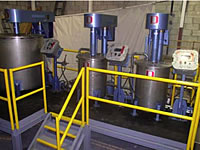 |
A
Dantco post mounted, variable speed disperser, Series 2030, 100 HP,
explosion proof, with 2 SS304 tanks with tapered bottom, mezzanine mounted,
with covers fill piping and flow meters, drain piping hooked-up to diaphragm
pumps, control panel with push button controls, digital tachometers and
ammeters. Visible also is the working platform built by the customer.
This heavy duty Disperser is used to process latex paint. |
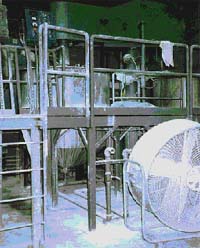 |
A
working platform serving aggregate bins. Notice the comfortable steps
leading to the solid steel deck and the removable railing built to OSHA
specifications. The platform was fabricated in modular form ready
to be assembled at the job site with simple tools. |
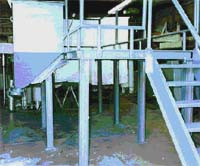 |
A
high pressure hot oil piping supply line used to heat rotating
drums in a textile production transfer printing press. The carbon steel
all welded pipe line with suitable insulation and expansion joints, originated
at the natural gas driven furnace with the hot oil flow being distributed
to various transfer printing machines by several pumps. Dantco was the
mechanical contractor responsible for design, procuring, installing,
integrating and validating all piping components and instrumentation. |
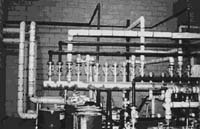 |
Piping
used to transfer resin from storage tank to various mixing tanks in a
paint factory. Notice the motor pumps, flow meters, various valves and
the threaded carbon steel piping. The supports and layout of all
components were dictated by cost constraints. |
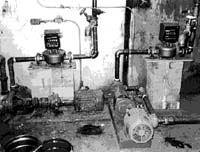 |
|